TFG Transfracht use Leapwork to modernize logistics software while supporting legacy systems
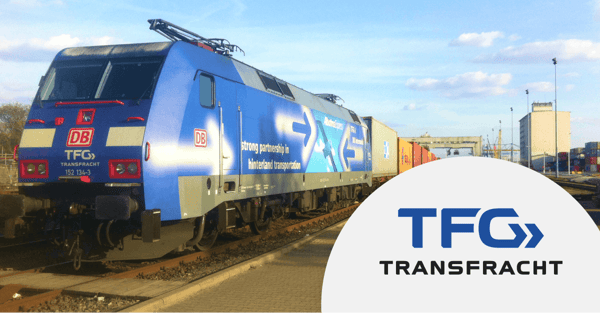
USE CASE
transforming logistics with automation
1 million
responsible for over 1 million Transport Units per year
100%
drastic reduction in manual testing time
1/1
accurate, live, and synchronized transport data
Challenge
Manual work is notorious within logistics. Handwritten receipts, infrequently updated ledgers, and the lack of standardized data sharing between ports, operators, and delivery contractors all create challenges.
At the same time, transportation is uniquely exposed to the volatility of traffic, weather, and geopolitical events.
Case in point: when the Ever Given blocked the Suez Canal for 6 days in March 2021, it single-handedly prevented over 350 transport ships reaching their destination, costing $9.6B USD worth of trade. For logistics companies like TFG Transfracht, it was essential to build reliable logistics models to increase the resiliency and efficiency of a shipment’s journey from the port to the shelf.
TFG Transfracht had a complex problem. They needed to modernize internal systems and create an integrated information chain that would provide accurate, up-to-date shipping information. And all of this had to work with the legacy systems used by third-party operators.
Solution
With so many integrated business partners to manage, TFG Transfracht’s data and monitoring projects initially required lots of developer and manual tester resources. This meant it was difficult to focus time and energy on system improvements. But with Leapwork, TGF Transfracht has empowered non-developers to introduce automation independently.
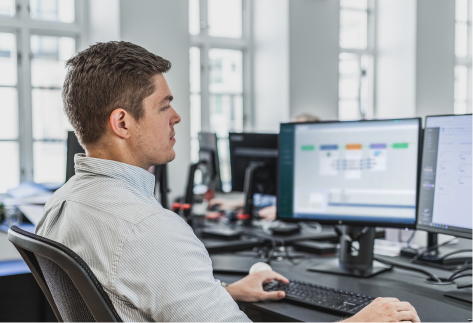
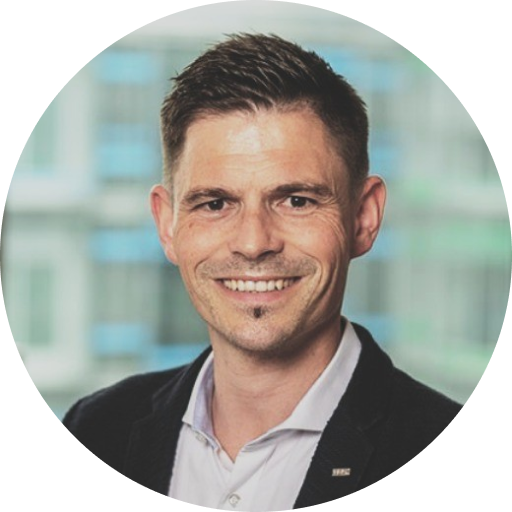
"The approach should not be to reduce your employees, but to ensure that they can focus on their real tasks. Their real task is not doing repetitive work but to raise the quality of our service offerings that we provide to our customers."
Impact
While TFG were modernizing internal systems, they still had to coordinate shipments by gathering information from legacy systems used by partners such as port operators. Previously, the vastly different data structures used by these operators required TFG employees to manually transfer data on shipments, arrivals, and departures.
Today, Leapwork makes it possible for TFG to automate every step of the data collection process, drastically reducing manual effort and, critically, ensuring that data is always up-to-date and accurate.
Time stamps, loading and discharge status, call signs, ship names and more are extracted automatically from operator systems and pulled into a report that acts as a single point of truth. This enables TFG Transfracht to pinpoint ship schedules and accurately predict arrival times for the full process chain, as goods travel by containers from the seaport, via long-haul trains, to a hinterland terminal then onwards by truck to their destination.
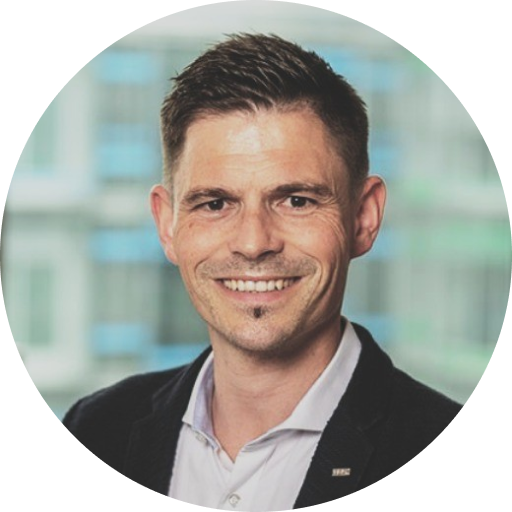
"Leapwork has enabled us to achieve seamless integration between our internal systems and those of our partners. The ability to automate data collection and testing has not only saved countless hours of manual effort but also ensured the accuracy and timeliness of critical logistics data. This has been a game-changer in delivering exceptional service to our customers while allowing our team to focus on innovation and continuous improvement."
More success stories
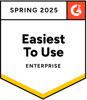
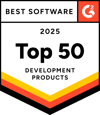
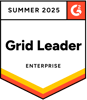